Tube and Pipe Weld Inspection Systems
Xiris weld inspection systems use proven laser-based vision system technology with high resolution, fast data capture and analysis rates to provide real-time detection of weld defects down to 0.015 mm in size.

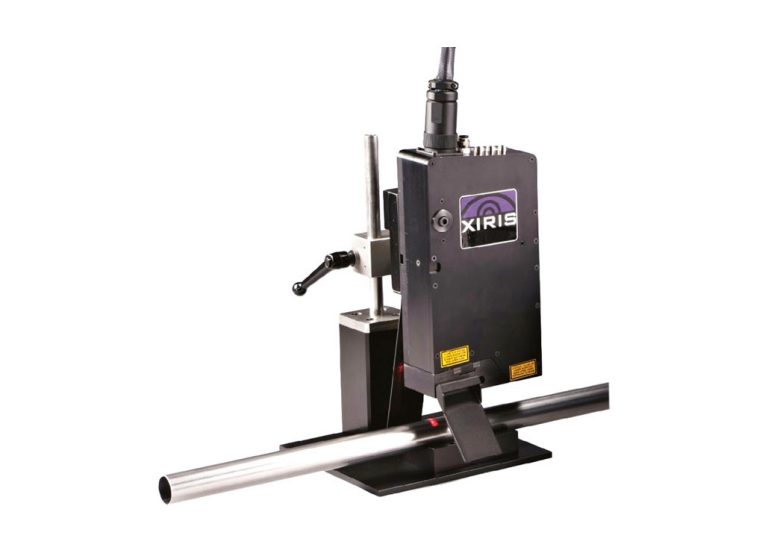
WI-2200
A laser-based 3D post-weld inspection system designed to detect quality issues related to the forming, welding and scarfing processes on Tube & Pipe mills with outside diameters of 5-200 mm (0.2-8″).
- Simplify and reduce mill set up time with real-time feedback on adjustments
- Improve weld quality, with 100% in-line monitoring right at the mill
- Non-contact, non-destructive sensors do not interfere with forming, welding and scarfing process
- Reduce operating costs with lower material scrap, customer returns and product liability claims
- Improved mill efficiency with real-time process monitoring, trend reporting, warning and alarms
- Air-cooled using factory air
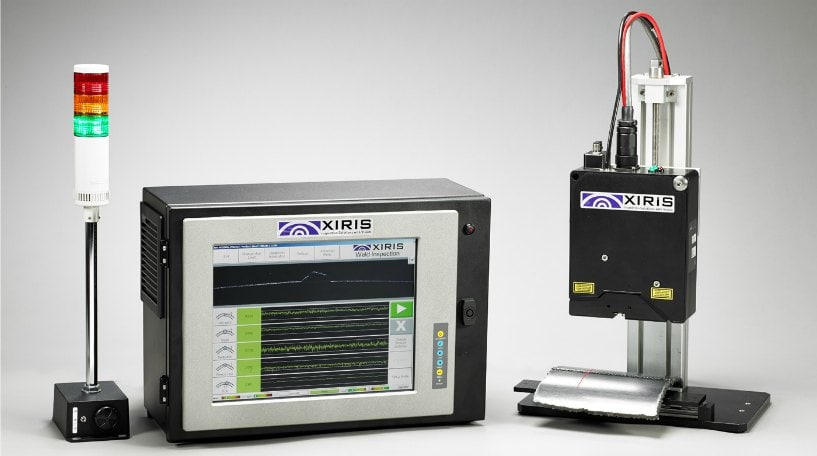
WI-3000
A laser-based 3D post-weld inspection system designed to detect quality issues related to the forming, welding and scarfing processes on larger High Frequency Tube & Pipe mills with outside diameters greater than 13 mm (1/24″).
- Simplify and reduce mill set up time with real-time feedback on adjustments
- Improve weld quality, with 100% in-line monitoring right at the mill
- Non-contact, non-destructive sensors do not interfere with forming, welding and scarfing process
- Reduce operating costs with lower material scrap, customer returns and product liability claims
- Improved mill efficiency with real-time process monitoring, trend reporting, warning and alarms
- Rugged water-cooled sensor
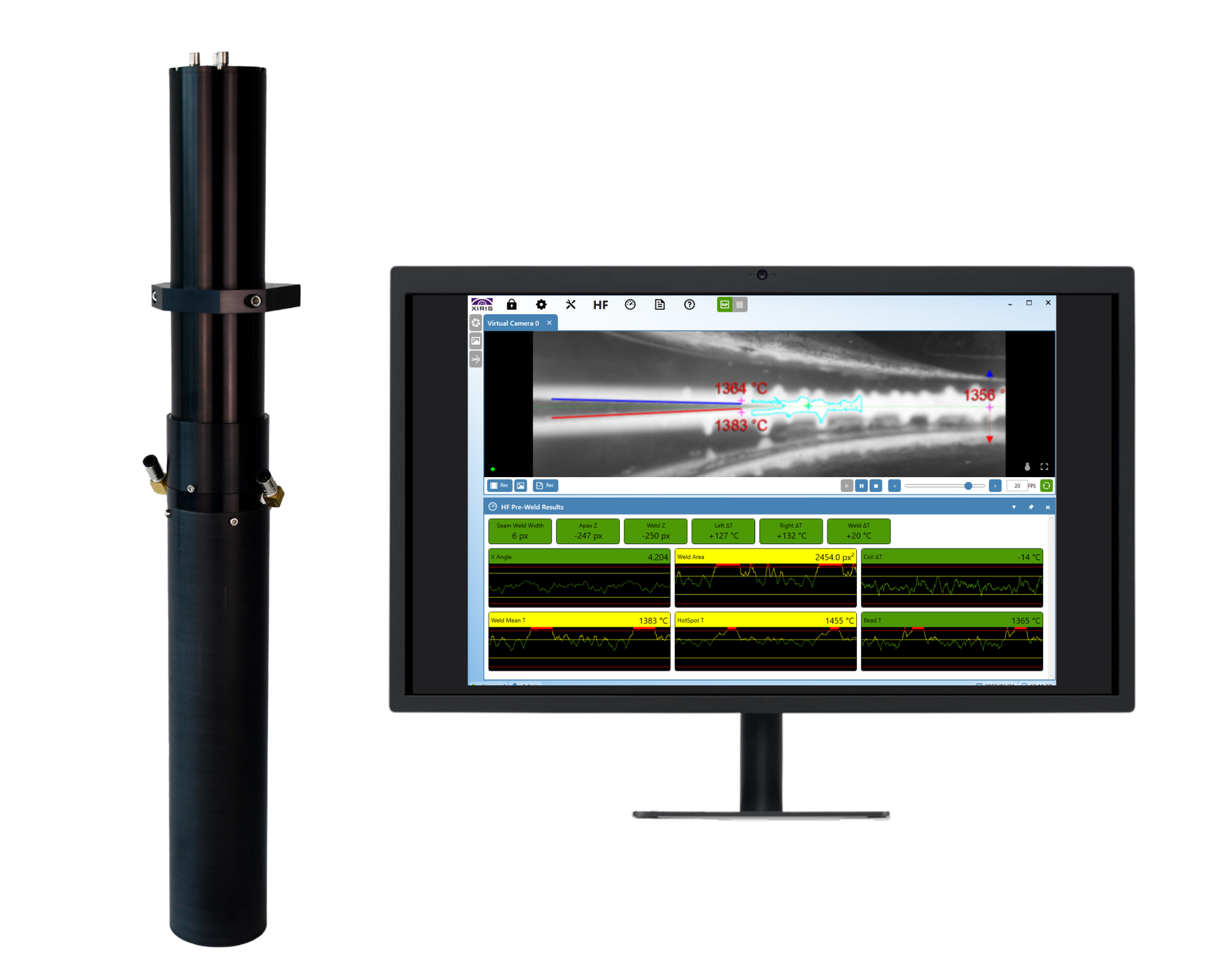
HF Pre – Weld Inspection System™
The Xiris HF Pre-Weld Inspection system enables operators to remotely monitor strip edges and the welding process of High-Frequency Tube Mills.
This solution, featuring the XIR-1800 thermal camera in a robust protective housing and an intuitive HMI computer, empowers you to achieve remarkable results on High-Frequency Tube Mills.
The HF Pre-weld system enables operators to remotely monitor strip edges and welding temperatures with ease.
Using advanced software, the system can measure, monitor, and record multiple process parameters, putting you in full control of your welding operations.
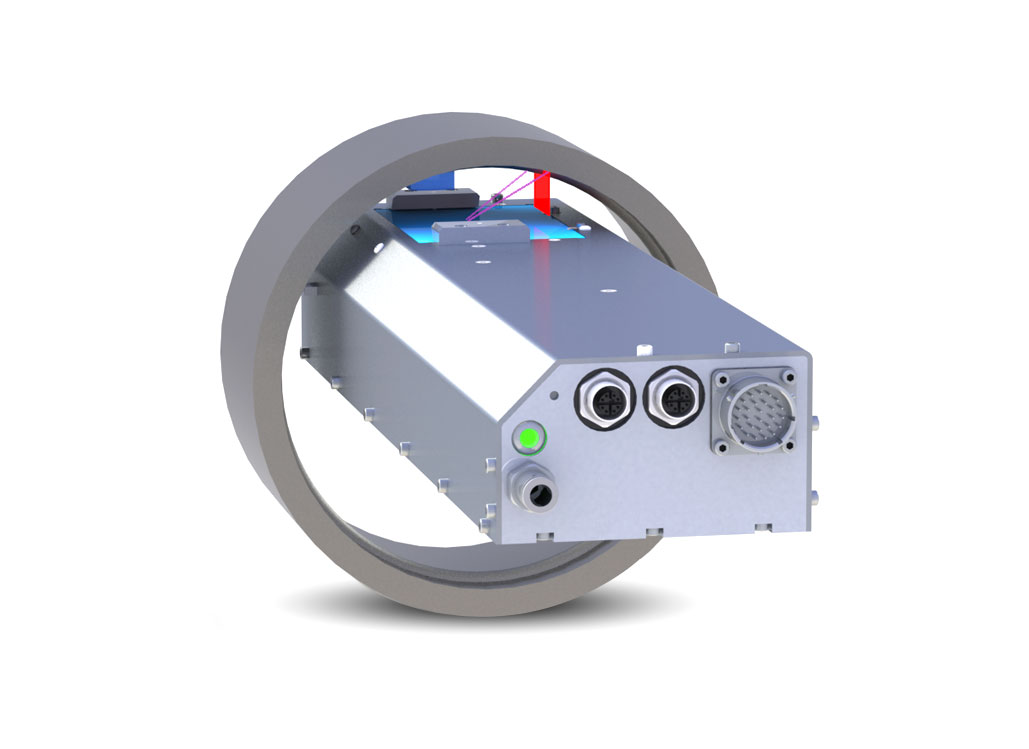
BeadScan
A sensor and image processing system for scanning, inspecting and recording the back side of a first pass weld bead, typically found in large welding projects such as pipeline construction, ship building, pressure vessel manufacturing or large pipe fabrication. Featuring:
- High resolution 2D image and a 3D shape profile generation of the entire weld bead
- Low-profile design fits inside pipes with ID >200mm
- Sensor head includes a high-resolution laser triangulation system and a high resolution 2D on-axis camera with its own specialized lighting
- Intuitive, easy to use software to fully inspect, analyze, annotate and record each weld
- Integrated bead profile inspection tools for advanced defect detection
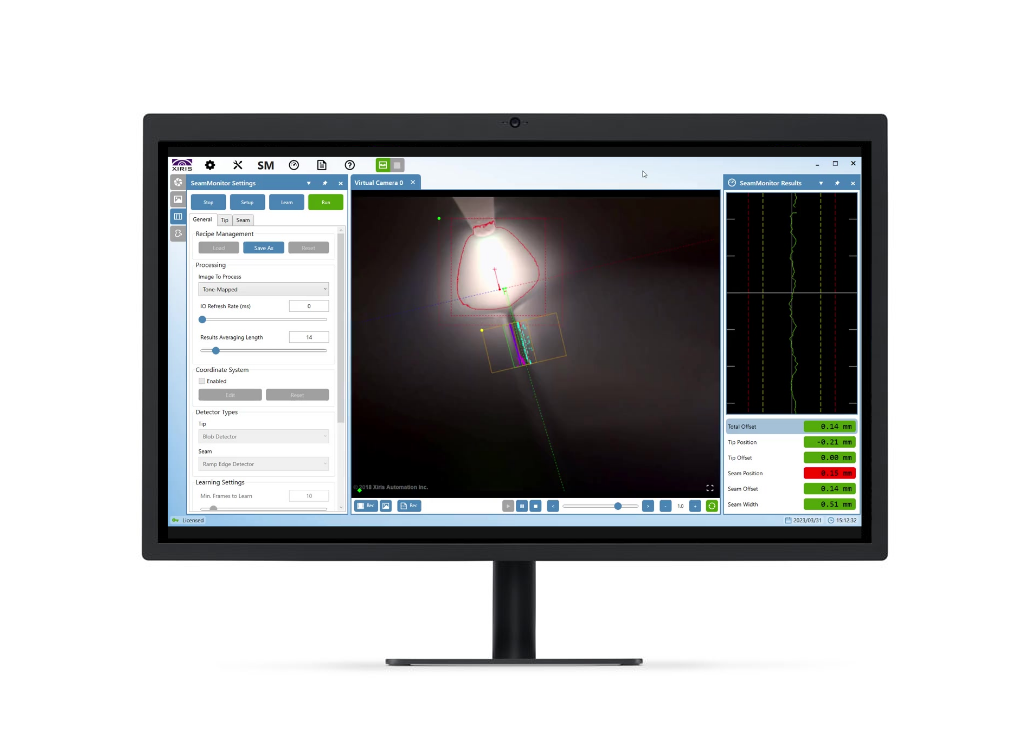
SeamMonitor™
The Xiris SeamMonitor™ system has been specifically developed to measure the seam alignment and weld seam width on TIG welded tube mills. Combining a High Dynamic Range (HDR) weld camera that can see a large range of brightness to easily capture the TIG torch, weld arc and weld seam, with sophisticated machine vision measurement software, SeamMonitor™ enables real-time monitoring of the weld seam size, the torch tip location, and the relative offset between the torch tip and its seam.
Interested in learning more about our weld inspection systems?
Join us for a video demo and info session